A Front Surface Mirror (FSM) is a type of mirror used for high-precision optical applications, usually using a 45° angle. The main feature is that the reflective layer is located on the front surface of the mirror rather than the back surface.
Unlike ordinary mirrors, where the reflective layer is located behind the glass, the light is not reflected until it passes through the glass, which results in some light loss and refraction. Front surface mirrors avoid this problem, allowing light to be reflected directly back after it is incident on the mirror surface, resulting in greater optical precision and efficiency.
Front Surface Mirror Technical Specifications
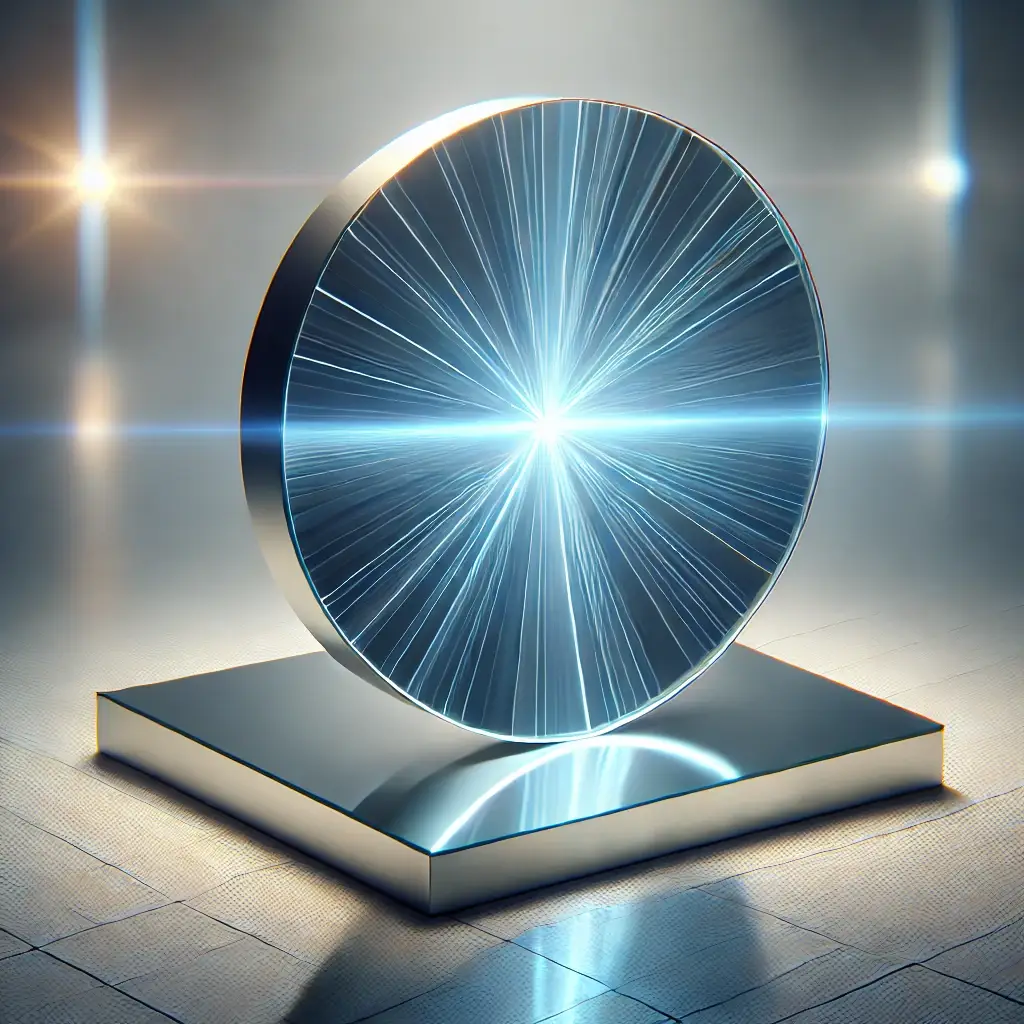
1. Standard Sizes
Manufacturers offer front surface mirrors in standard sizes, typically ranging from small mirrors with a diameter of 5 mm to large mirrors up to 85 mm. Rectangular and square mirrors range in size from 1 mm x 1 mm to 85 mm x 85 mm. These standard sizes meet common needs across a wide range of industries, ensuring that users can easily find a mirror that meets their requirements.
For special applications, customization options are available, with companies such as Optolong offering custom optics that allow users to specify unique configurations. This flexibility includes fabricating round, rectangular, and square substrates to meet specific needs. Customization ensures that professionals in fields such as scientific research and industrial applications get the precise front surface mirrors they need for optimal performance.
2. Coating Types
Front surface mirrors are available with a variety of coating options, each tailored to a specific application. Common coatings include UV-enhanced coatings, dielectric coatings, silver coatings, and gold coatings.
These coatings determine the reflectivity and wavelength range of the mirror, making it suitable for a variety of uses. For example, dielectric coatings offer high reflectivity over a wide spectral range, while silver and gold coatings offer excellent performance in specific wavelength ranges.
3. Structure and Working Principles of Front Surface Mirrors
The key to a front surface mirror is its special reflective coating. This coating is attached directly to the front of the mirror and is usually made of highly reflective materials such as aluminum, silver, and gold.
Without the obstruction of a transparent base layer, front surface mirrors reflect incident light with maximum efficiency and avoid the “ghosting” phenomenon that is common with ordinary mirrors.
The advantages of front surface mirrors over conventional rear surface mirrors are:
- High reflectivity: Front surface mirrors reflect up to 98% of the incident light.
- Elimination of light loss: Since the reflecting surface is directly in front, no light has to pass through a transparent medium such as glass, so energy loss is reduced.
- Reduced optical aberrations: Front surface mirrors avoid optical aberrations caused by the passage of light through glass media and are therefore widely used in high-precision optical instruments.
- Reduced light loss: Since the light is directly reflected on the front surface of the mirror, it does not go through the secondary reflection of the glass, so the light loss and reflection blurring are reduced.
- Avoiding ghosting phenomenon: Traditional mirrors produce ghosting of light reflected through the glass, while front surface mirrors avoid this problem because the light is directly reflected on the coating of the mirror.
- Applicable to a wide range of spectral ranges: Front surface mirrors can be customized with different coating materials to give better reflective properties in different spectral ranges (e.g. UV, visible, and infrared).
Applications for Front Surface Mirrors
1. Cameras and Telescopes
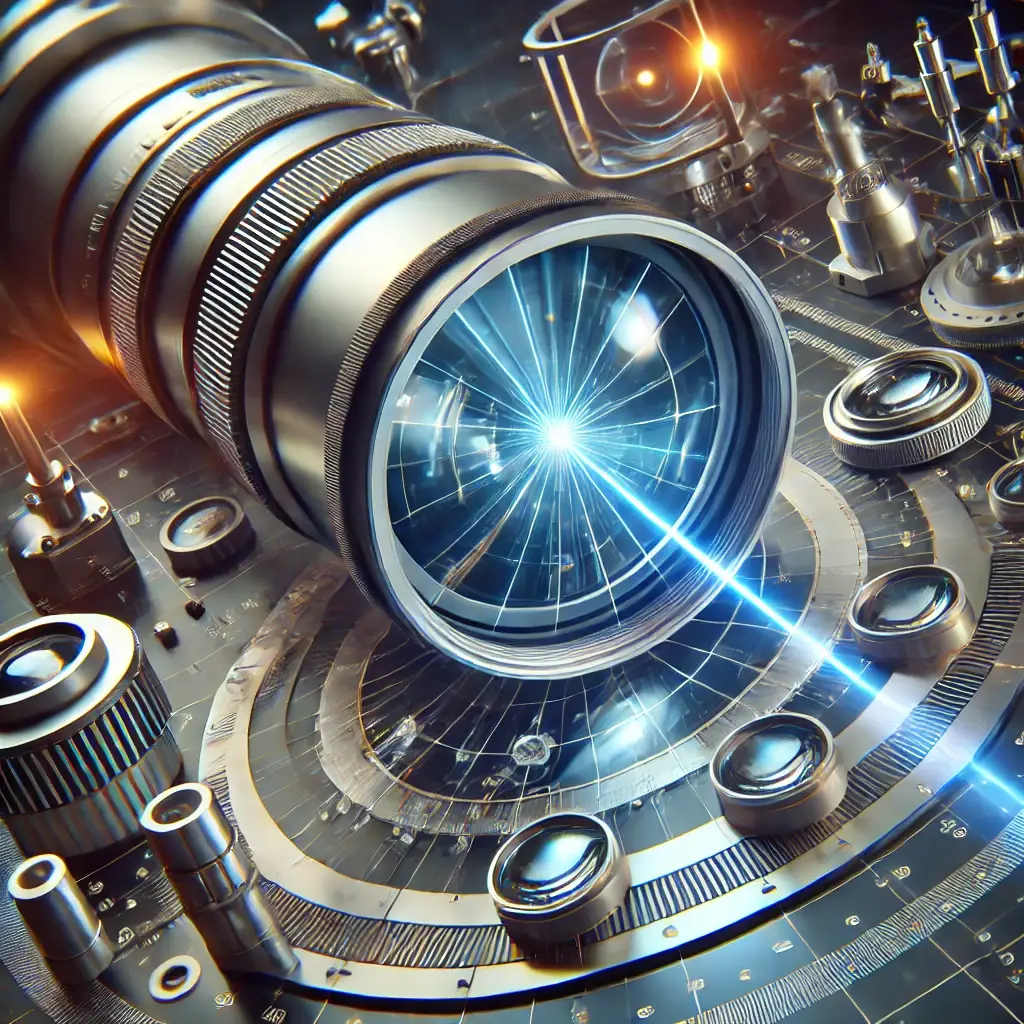
Front surface mirrors play a vital role in cameras and telescopes. They provide clear, sharp reflections, which are essential for capturing high-quality images.
Photographers and astronomers rely on these mirrors for precise focus and detail. Direct reflections minimize distortion, which improves overall image quality.
2. In Scientific Research
In scientific research, front surface mirrors contribute greatly to accurate data collection. Researchers use them in a variety of optical instruments to ensure accurate measurements and observations.
Their ability to reflect light without distortion makes them indispensable in experiments that require high precision.
3. Medical Equipment
Medical devices benefit greatly from front surface mirrors. They improve the clarity of images in diagnostic equipment such as endoscopes and microscopes.
This clarity helps medical professionals make accurate diagnoses and treatment plans. The excellent reflectivity of the mirrors ensures that even the smallest details are visible.
4. Industrial Applications
In industrial environments, front surface mirrors improve automation and quality control processes. They provide precise reflection in laser systems and optical sensors, ensuring accurate alignment and measurement.
Industries such as manufacturing and robotics utilize these mirrors to improve the efficiency and accuracy of their operations.
5. Comparison with Other Optical Mirrors
In addition to front surface mirrors, other types of optical mirrors have their special uses. For example, dichroic mirrors are optical elements that selectively reflect and transmit light based on wavelength, and are commonly used in fluorescence microscopy and other applications that require the separation of different wavelengths of light. Dichroic mirrors control the reflection and transmission of light at different wavelengths by coating the mirror surface with multiple layers of thin film.
In contrast, the primary function of a front surface mirror is to reflect incident light to the greatest extent possible without distinguishing between wavelengths. This gives it a unique advantage in highly reflective application scenarios such as lasers and telescopes. Dichroic mirrors, on the other hand, are more commonly used for wavelength selection and separation applications, such as biomedical imaging and spectral analysis.
6. Care and Maintenance of Front Surface Mirrors
Users should follow the manufacturer’s instructions to avoid damaging the coating during cleaning. Proper maintenance will extend the life of the mirror and maintain its excellent reflectivity and image clarity.
Despite their excellent optical performance, front surface mirrors are susceptible to contamination and damage because their front surfaces are directly exposed. To ensure that front surface mirrors last a long time and work efficiently, here are some maintenance recommendations:
- Regular cleaning: Wipe the mirror gently with a lint-free cloth and a special cleaner to avoid scratching the coating.
- Avoid moisture: The optical coating of front surface mirrors is sensitive to moisture. Prolonged exposure to humidity may lead to oxidation and damage to the coating, so they should be stored in a dry environment.
- Handle gently: minimize direct pressure on the mirror surface during use and cleaning to avoid scratches or peeling of the coating.
To summarize
Front surface mirrors offer numerous advantages, including excellent reflectivity and image clarity. These properties make them essential in areas such as imaging, scientific research, and industrial applications. Their potential use also extends to medical devices and automated systems where accuracy is critical.
Optolong’s optical filters complement these mirrors by enhancing imaging capabilities. Their customizable options and advanced coatings ensure optimal performance in a variety of applications. By combining front surface mirrors with Optolong’s filters, professionals can achieve better visual output, taking their work to new heights of accuracy and detail.
Related reading: Dichroic Mirrors Vs Beamsplitters