Optical coatings play an important role in a variety of technological applications, including astronomy, photography, laser technology, and consumer electronics. These coatings can enhance the reflective, transmissive, or absorptive properties of optical components such as lenses, mirrors, and filters.
As the demand for advanced optical systems continues to grow, it becomes increasingly important to understand the basics and future developments in optical coatings. This article will explore the basics of optical coatings, their applications in various industries, and emerging trends and future developments in the field.
What are optical coatings?
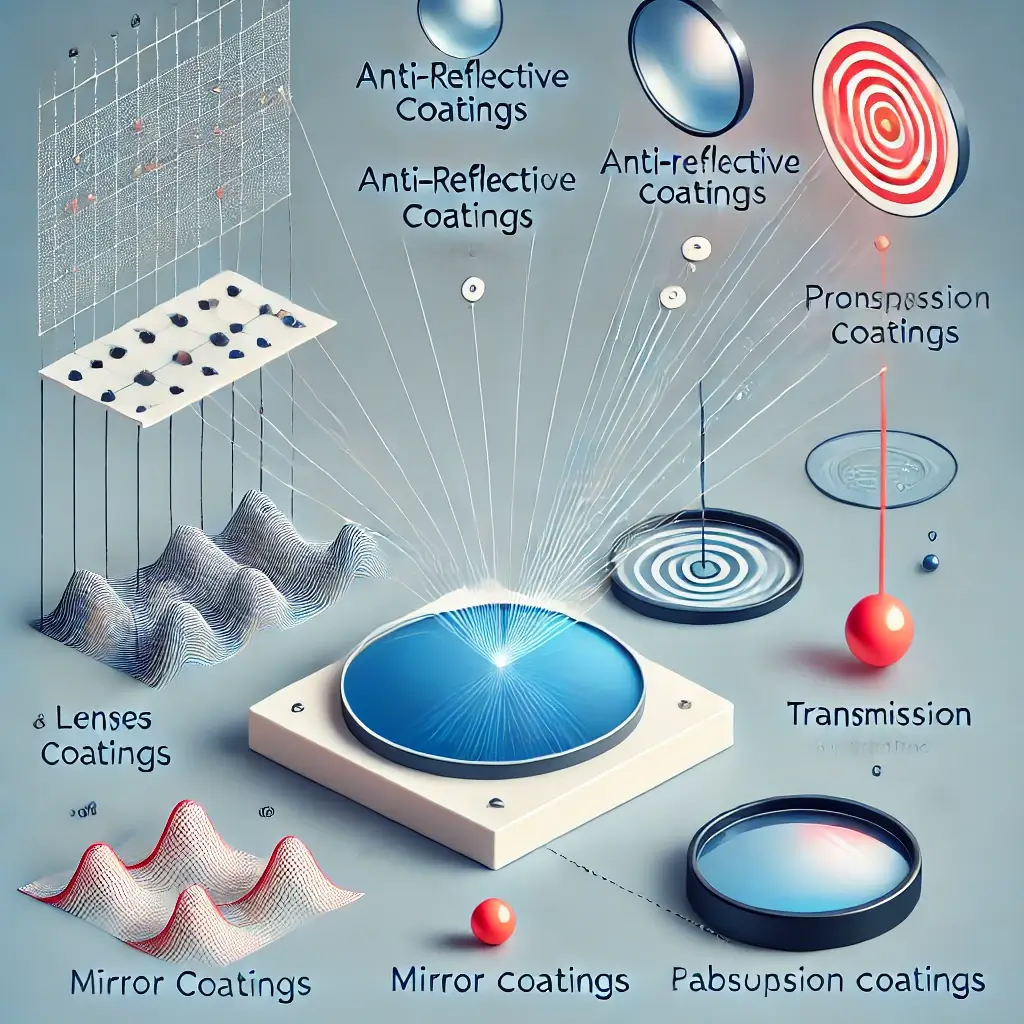
Optical coatings are thin layers of material deposited on optical components such as lenses, mirrors, and filters to modify their optical properties.
These coatings can enhance transmittance, reduce reflection and selectively filter specific wavelengths of light. The performance of an optical coating depends on factors such as the number of layers applied, the thickness of each layer, and the material used.
There are many types of optical coatings, each with its unique uses:
- Anti-reflection (AR) coatings: Reduce surface reflections and enhance the transmission of light through lenses and other optical components.
- Reflective coatings: Increase the reflectivity of mirrors and other reflective surfaces, commonly used in telescopes and laser systems.
- Filter coatings: Selectively transmit or reflect certain wavelengths of light, used in photography, scientific instruments, and telecommunications.
- Beam Splitter Coatings: Beam splitter coatings can split an incident light beam into two or more beams, reflecting and transmitting light in predetermined proportions. Used in lasers, interferometers, and optical measurement equipment.
1. Materials used for optical coatings
The materials used for optical coatings determine the effectiveness and durability of the coatings, and we should also pay special attention when choosing. The more common materials include:
- Silicon dioxide (SiO2): Due to its low refractive index and excellent transparency, it is widely used in anti-reflective coatings.
- Aluminum oxide (Al2O3): Known for its hardness and chemical resistance, it is used in coatings that require durability.
- Magnesium fluoride (MgF2): Due to its good UV transmission performance, it is often used in anti-reflective coatings for lenses and displays.
Advanced optical coatings can also use nanomaterials or composite materials to achieve specific optical properties, such as enhanced reflectivity or improved environmental resistance.
2. Manufacturing process of optical coatings
The production of optical coatings involves a variety of complex technologies to ensure precision and quality. The most common methods include:
- Physical vapor deposition (PVD): A process in which materials are evaporated in a vacuum and then condensed onto an optical surface. PVD techniques include thermal evaporation, electron beam evaporation, and sputtering.
- Chemical vapor deposition (CVD): A technique for depositing materials as thin films through chemical reactions. CVD is particularly useful for producing coatings that are complex in composition or require high purity.
- Ion Assisted Deposition (IAD): A variation of PVD that uses an ion beam to bombard the coating material during deposition, thereby improving film density and adhesion.
Critical parameters such as coating thickness, deposition rate, and substrate temperature must be tightly controlled to achieve the desired optical properties.
Applications of Optical Coatings
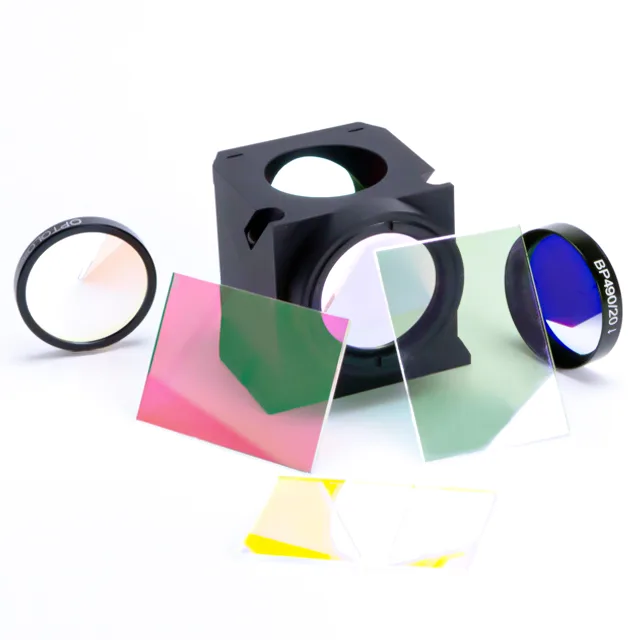
1. Astronomy and Photography
In astronomy, optical coatings improve the performance of telescopes and other observation instruments. Antireflective coatings minimize light loss and maximize the transmission of light through lenses and mirrors, enabling clearer, more detailed images of distant celestial objects. Similarly, high-quality reflective coatings are used on telescope mirrors to improve reflectivity and image clarity.
In photography, optical coatings are used on camera lenses to reduce glare and ghosting and to improve image contrast and color fidelity. Special coatings, such as ultraviolet (UV) and infrared (IR) filters, are also used to block unwanted wavelengths and protect lenses from environmental damage.
2. Laser Technology
Coatings such as high-reflectivity (HR) coatings are applied to laser mirrors to maximize reflectivity and minimize energy loss. Antireflective coatings are used on laser lenses and windows to prevent back reflections that could damage the laser source or degrade beam quality.
In high-power laser systems, optical coatings must also provide thermal and mechanical stability to withstand the high intensity of energy. This requires the use of advanced materials and coating technologies to ensure durability and reliability under extreme conditions.
3. Microscopes
In microscopes, optical coatings such as anti-reflection coatings are used to reduce light reflection and increase light transmittance, thereby enhancing the brightness and clarity of images. These coatings are particularly important for the performance of microscope objectives and eyepieces, especially in low light conditions or at high magnification, which can significantly improve image quality.
In addition, beam-splitting coatings are used in fluorescence microscopes to accurately separate and combine light beams of different wavelengths, ensuring effective separation of excitation light and emission light. This coating technology helps to obtain high-contrast fluorescence images, making microscopic observations more detailed and accurate.
3. Consumer Electronics and Eyewear
In consumer electronics, optical coatings enhance the performance of devices such as smartphones, tablets, and VR headsets. Anti-reflective coatings reduce glare on screens, improving visibility in bright environments. Similarly, coatings that block blue light or enhance contrast can be used to improve user experience and reduce eye fatigue.
For eyewear, optical coatings are both functional and aesthetic. Anti-reflective coatings reduce reflections on eyeglass lenses, improving visual clarity and comfort. Blue-light blocking coatings protect eyes from harmful digital screen radiation, while mirrored coatings add a stylish reflective finish to sunglasses.
Future Development of Optical Coatings
1. New Materials and Technologies
The future of optical coatings lies in the development of new materials and deposition techniques. Researchers are exploring the use of nanomaterials and composites to create coatings with unique optical properties, such as ultra-high reflectivity or superior transparency. Multilayer coatings and ultra-thin coatings are also being developed to achieve more precise control over light transmission and reflection.
Advances in atomic layer deposition (ALD) and molecular beam epitaxy (MBE) are expected to enable the production of more complex coatings with superior performance characteristics. These technologies allow atomic-level control of coating thickness and composition, paving the way for new applications and innovations in optical coatings.
2. Smart Coating Technologies
The advent of smart coatings represents a major advance in optical coating technology. Adjustable and adaptive coatings are being developed to change their optical properties in response to external stimuli such as temperature, light intensity, or electric fields. This capability could lead to the development of smart lenses and adaptive optics for advanced imaging systems, sensors, and consumer devices.
Smart coatings can also enable real-time optimization of optical systems, improving performance in dynamic environments and reducing the need for manual adjustments.
3. Improved environmental resistance and durability
Future developments in optical coatings will also focus on improved environmental tolerance and durability. Coatings with enhanced scratch resistance, corrosion resistance, and thermal stability are currently being developed to extend the life of optical components in harsh environments, such as space, deep sea exploration, and desert conditions.
These advances will require the use of new materials and innovative coating technologies, such as diamond-like carbon (DLC) coatings and nanocomposite coatings, to provide superior protection without compromising optical performance.
Conclusion
Optical coatings are an integral part of modern technology, improving the performance and functionality of optical components across a wide range of industries. From astronomy and photography to laser technology and microscopy and consumer electronics, these coatings provide key advantages that drive innovation and progress.
As technology advances, the future of optical coatings will be driven by the development of new materials, smart coating technologies, and better environmental tolerance. These advances are expected to unlock new applications, improve performance, and provide unprecedented functionality, ensuring that optical coatings remain at the forefront of technological innovation.
What can Optolong bring to you?
Optolong offers a wide range of high-quality optical coatings and filters designed to improve performance in a variety of applications.
Optolong’s products feature advanced optical coatings such as anti-reflective coatings that maximize light transmission and reduce glare, narrow-band and broadband filters for precise wavelength selection, and specialized coatings for increased environmental resistance and durability.
Related reading: How Dichroic Mirrors Split Light?