Ultrasonic cleaning before coating refers to the removal of dust, oil stains, imprints, etc. on the substrate by physical methods to ensure better combination of substrate and coating and smooth production. Cleaning is an indispensable process before PVD, and it is also the most important process in production. Once there is a problem with cleaning, not only will it not be able to provide products that meet the requirements, but it is likely to lead to customer complaints and compensation. Therefore, cleaning is particularly important and must be done with caution.
So what are the factors that affect the quality of cleaning? Cleaning time, cleaning solution, mechanical action and temperature, these four factors are mutually influencing, the weakening of one factor can be compensated by enhancing the effect of the other three factors, and vice versa. Among these four factors, the minimization of cleaning time is also the goal, which can improve the efficiency of cleaning.
The main cleaning methods and steps include: soaking in cleaning solution and ultrasonic cleaning, rinsing and drying. But the Optolong 12-tank ultrasonic cleaning machine has a special feature: only pure water is needed for cleaning, no cleaning fluid is required.
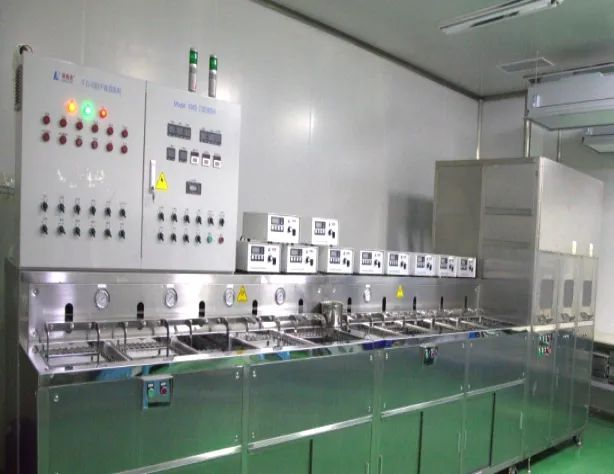
Ultrasonic cleaning focuses on ultrasonic waves.
- Ultrasound is a sound wave with a frequency above 20kHz beyond the range of human hearing. The propagation of ultrasonic waves depends on the elastic medium.
- When it propagates, the particles in the elastic medium oscillate, and energy is transmitted through the medium in the direction of propagation of the ultrasonic waves.
- This kind of wave can be divided into longitudinal waves and transverse waves. In solids, both can be transmitted, while in gases and liquids, only longitudinal waves can be transmitted. The vibration of air bubbles can also scrub solid surfaces. Air bubbles can also “drill” into cracks to vibrate, causing dirt to fall off. For greasy dirt, due to ultrasonic cavitation, the two liquids are rapidly dispersed and emulsified at the interface.
- When the solid particles are wrapped by the oil dirt and adhere to the surface of the cleaning piece, the oil is emulsified and the solid particles will fall off. Cavitation bubbles can cause high velocity gradient and viscous stress on the surface of the vibrating bubbles, which promotes the destruction and shedding of dirt on the surface of cleaning parts.
- The high-speed micro-jets generated by ultrasonic cavitation on solid and liquid surfaces can remove or weaken the boundary. The dirt layer corrodes the solid surface, increases the stirring effect, accelerates the dissolution of soluble dirt, and strengthens the cleaning effect of chemical cleaning agents.
Rinsing the substrate
The next step is rinsing, which is designed to thoroughly remove any remaining cleaning fluid or other contaminants from the substrate, making the substrate cleaner before drying. Once there is residue on the substrate, it will be difficult to clean up after drying.
Drying the substrate
The final step is to dry the cleaned substrate in a drying oven. Therefore, the baking temperature must be greater than 100 °C, preferably between 110 °C and 130 °C, so that the water can be quickly evaporated and dried. After drying, the temperature of the workpiece is too high and it takes a long time to cool down.
Optolong uses a twelve-slot ultrasonic cleaner to clean the substrate, and the hard-coated fluorescent filter has the following characteristics:
1) A single piece of glass is coated with a hard film on both sides;
2) High transmittance, bright signal;
3) Deep cut-off OD>5, dark background, no color;
4) The wavelength is stable and does not drift;
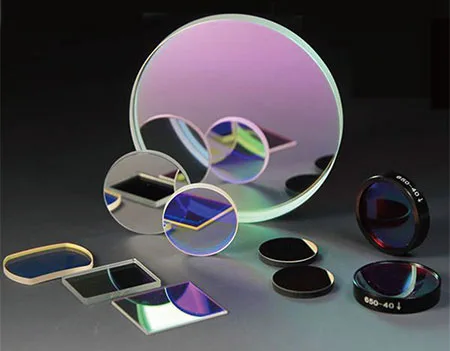