In the field of optics, flatness determines the performance and efficacy of various optical components such as mirrors, lenses, and windows. This property defines the accuracy with which a surface is aligned with an ideal plane and is not only a measure of quality but a fundamental criterion that affects the entire optical system.
This article will delve into the application of flatness in optics, how to measure flatness, and what to consider when choosing the surface flatness of an optical system. Let’s read it together!
At the same time, types of optics in the field of optics has also become essential knowledge for many students.
What is Flatness?
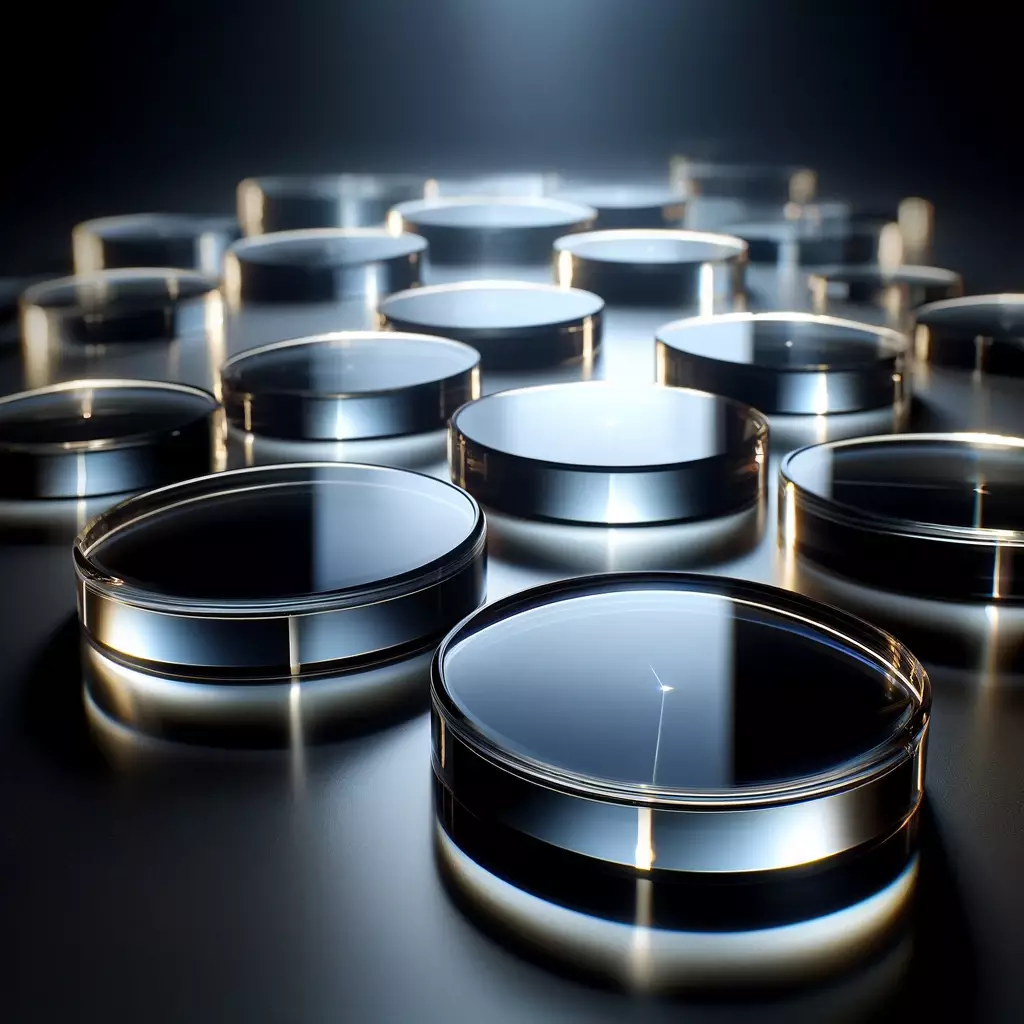
In optics, flatness refers to the precision with which a surface matches a perfect plane, minimizing deviations that could affect the performance of optical systems.
It impacts the integrity of light paths in applications such as imaging, interferometry, and laser systems. Therefore, proper flatness reduces aberrations and improves the overall quality and functionality of optical devices.
What Are the Accuracy of Flatness?
The accuracy of optical flatness is often specified as a fraction of the wavelength of light used in the system, with common standards being λ/4, λ/10, λ/20 or even λ/100 for very high accuracy applications.
For applications involving high-resolution imaging, advanced scientific research, or within systems such as aerospace, where greater accuracy (smaller wavelength fractions) is required, even the smallest deviation can significantly impact performance.
How Optical Flatness Works?
Optical flatness works by ensuring that the surfaces of optical components, such as lenses and mirrors, are precisely aligned with perfectly flat surfaces. Minimizes deviations that can cause optical aberrations, thereby maintaining accuracy and predictability of the behavior of light in optical systems.
Any deviation from this accuracy can cause optical aberrations, image distortions, and interruptions in the optical path. Flatness is typically measured as a fraction of the wavelength of light using precision instruments such as interferometers, which highlight the tiniest deviations from perfect flatness. This allows the optical system to be precisely tuned to optimize its functionality and reliability.
Applications of Optical Flatness
Imaging System
In equipment such as telescopes, microscopes, and cameras, the optical flatness of lenses and mirrors ensures that the entire light path is not deflected, thereby maintaining image fidelity.
This precision prevents optical aberrations such as blur or distortion, effectively improving high-resolution imaging in scientific research and photography.
Laser System
Optical components in laser systems, such as mirrors and beam splitters, require a high degree of flatness to accurately guide and focus the laser beam.
This precision is often used in applications such as laser cutting and medical surgery, where the path and focus of the beam determine the quality and safety of the operation.
If you need to know about related products of dichroic mirrors, you can read this article What is a dichroic mirror?
Interferometry
In interferometry, this technique involves the superposition of waves to measure small distances and shapes, relying on optical planes to create precise reference planes. It is used in areas such as metrology, semiconductor manufacturing, and materials science.
Telecommunications
In telecommunications, especially fiber optics, flat optical components help to efficiently transmit optical signals over long distances. This flatness ensures minimal signal loss and distortion, maintaining the integrity and speed of data transmission.
Observatory
Telescopes used in astronomy rely on mirrors with extremely precise flatness to accurately reflect light from distant stars and galaxies. This accuracy helps astronomical research and discovery produce clear, detailed images of celestial objects
Scientific Research
Various scientific experiments, especially physics and chemistry experiments, utilize optical planes to manipulate and measure light with high precision.
Telescopes require extremely flat mirrors to accurately reflect and focus light from distant objects to achieve clear and detailed astronomical observations.
These applications highlight the importance of optical flatness in ensuring the efficiency and effectiveness of technologies that rely on precise light manipulation and measurement.
Things to Consider When Choosing Optical System Surface Flatness
- High-precision applications such as photolithography require extremely flat surfaces (e.g., λ/20 or better) for optimal performance.
- Shorter wavelengths require greater flatness due to greater sensitivity to surface irregularities.
- Systems sensitive to image degradation require greater flatness to minimize aberrations such as astigmatism and coma.
- Choose materials with high thermal stability and low coefficient of expansion to maintain flatness under varying conditions.
- Choose designs and materials that are resistant to environmental changes such as temperature fluctuations and mechanical stress.
- Consider the limitations of manufacturing accuracy, which may affect the achievable flatness.
- Ensure that appropriate measurement techniques are used to verify flatness during and after production.
By carefully considering these factors, you can choose the surface flatness of your optical system to ensure functionality and performance.
How is Surface Flatness Measured?
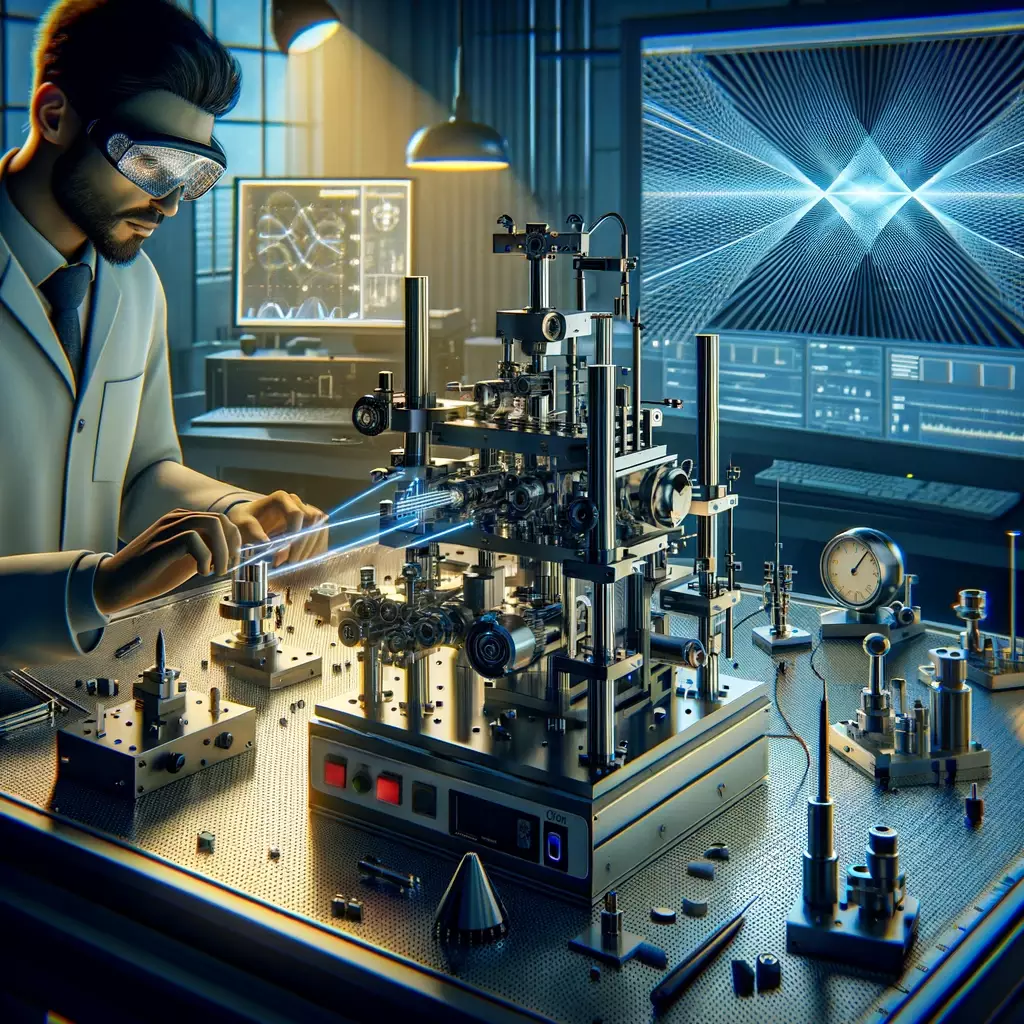
To accurately measure the flatness of optical surfaces, you first need to ensure that the working environment is clean and vibration-free. After cleaning the optical plate, place it gently on the surface of the object to be measured. Here is a detailed step-by-step guide on how to perform this measurement:
Step 1: Set Up the Interferometer
Prepare the equipment: Set up the interferometer according to the manufacturer’s instructions. This usually involves ensuring that all components, such as light sources, beam splitters, and detectors, are properly aligned.
Select a reference surface: Use a known high-precision flat surface as a reference. Ideally, the reference surface should be of better quality than the surface being measured.
Step 2: Prepare the Test Surface
Clean the surface: Make sure the optical surface to be tested is free of dust, oil, or any other contaminants. Use appropriate cleaning solutions and techniques suitable for optical surfaces.
Position the test surface: Place the optical component to be tested within the path of the interferometer. The surface should be perpendicular to the direction of the incident beam.
Step 3: Take Measurements
Illuminating the surface: Turning on the interferometer’s light source, usually a laser that emits coherent light. Make sure the beam covers the test surface evenly.
Capture the interference pattern: Light reflected from the test surface will interfere with light reflected from the reference surface. This interference pattern is captured by the detector.
Step 4: Analyze the Data
Interpret interference fringes: The interference pattern will appear as a series of dark and light fringes. Each fringe represents a profile of constant optical path difference, which is related to the deviation from the flatness of the surface.
Software Analysis: Use software to analyze stripe patterns. The software can convert these patterns into surface topography maps that quantitatively display deviations from flatness.
Step 5: Tune and Retest
Make adjustments: If the surface does not meet the required specifications, make necessary adjustments such as repolishing or regrinding the surface.
Repeat Measurements: After adjustment, repeat measurements to verify that the desired flatness has been achieved.
Step 6: Record and Report
Record results: Record all measurement results, including interference patterns and quantitative analysis. The documentation should detail the measurement setup, conditions, and final flatness achieved.
Reporting: Create a detailed report summarizing findings and compliance with specifications for quality control or further manufacturing processes.
By performing the following steps, you can accurately measure and verify the flatness of optical surfaces to ensure they meet the precise operating requirements of a variety of high-precision optical applications.
Summarize
Flatness in optics is a fundamental property that defines how closely an optical surface conforms to a perfectly flat surface. This feature ensures the accuracy and efficiency of the optical system by minimizing deviations that can cause aberrations and distort light propagation.
Measuring and maintaining the correct flatness of optical components such as lenses, mirrors, and windows enables the required performance and reliability in these complex systems.
If you still have any questions during the reading process or need to purchase related optical filters, please contact Optolong Optics. We have professional staff to answer your questions and serve you.